Moisture tracer analyzer MT1000
(Für uA Chlorgas und Phosgen)
The MT1000 has been particularly designed for applications, which are too demanding for other moisture analyzers. HCI environments and chloride gases mean no problem for the MT1000. Measurements can be taken in all gaseous environments, which do not react with phosphoric acid. One analyzer is able to monitor up to 3 sensors.
Because of the separated sensor and at additional use of ZENER safety barriers the MT1000 can also be used in ATEX areas.
The sensors of the moisture tracer MT1000 can be supplied with compression fittings or internal screw threads. The measuring principle is absolute and does not require any calibration or zero point adjustment. By pressing a button the sensor is able to do a self-test in order to check if it has to be recoated. The coating of the sensor can be carried out by the customer himself.
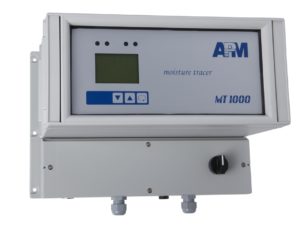
Moisture tracer MT1000 - Information
The measuring range is pre-set by the factory to 0…2000 ppm and can be changed by customer, if requested.
The MT1000 can be supplied in various casing versions. The wall mounting version is the most common one.
- bench mount version – stand-alone unit
- field casing
- 19″ rack mount
- Power supply: 90…250 V/AC, 50…60Hz
- Analogue outputs 0/4…20mA (one analogue outper per channel)
- Alarm outputs (changeover)
- RS232/RS484 /Profibus
The analyzers can be supplied with 1, 2 or 3 measuring channels and sensors. Further accessories can be supplied on customer’s request.
This is for example:
- Accessory for ATEX applications
- Complete sample gas path on mounting plate or in a cabinet
- Air-conditioning for mounting in a cabinet
- Flowmeters resistant againt chloride and phosgene
- Valves resistant against chloride and phosgene
- Accessories for mounting and installation
Moisture trace analyzer MT1000 - Applications and benefits
Typical applications
- Additive manufacturing
- Aluminium industry
- Analysis of gas storage
- Food and beverage industry
- MAP packaging monitoring
- Glass production
- Inert glove boxes
- Semiconductor industry
- Bond furnaces
- Inert gas regulation
- Ceramics
- Adhesive industry
- Soldering equipment
- Pharmaceutical industry
- Thermal after-burning
- Sinter and reflow furnaces
- Heat treatment
- Petro and polychemistry
- Pyrolysis processes
- Reflow furnaces
- Welding equipment
Benefits at a glance
- Long lifetime of the sensors
- Extremely quick response times
- Good reproducibility of measuring values
- Low measurement inaccuracy (<2% of measuring value)
- Numerous configuration options
- Hydrogen-resistant
- Saving costs by inert gas regulation
- Maintenance and calibration in Germany
- Insensitive against vibrations and positions
- Good readability
User-friendly
Sample gas conditioning on customer's request
Up to 3 sensors at one analyzer